Intercompany stock transfer process in SAP is a process of transferring goods between two plants belonging to different company codes. The process involves creating a stock transport order (STO) in SAP ERP system. The STO is a document that contains information about the goods to be transferred, such as material number, quantity, and delivery date. Once the STO is created, it is sent to the receiving plant for processing. The receiving plant then creates a goods receipt (GR) against the STO when the goods are received. Finally, an invoice is created by the supplying plant and sent to the receiving plant for payment.
In this document, following scenario is covered in detail with screenshots:
- Customer places order to depot or salesman. Depot in charge forwards the order to corresponding sales in charge
- All such orders from customers (against a depot) and from depots are to be cumulated and entered in SAP. Use Transaction code – ME21N.
- Warehouse in charge reviews the pending order report. Use transaction VL10I. The report displays the delivery quantity along with stock available quantity.
Warehouse in-charge decides the order to be executed today and create delivery document directly from pending order report. - Packing in charge reviews the packing due list report VL10P. He then selects the delivery order and allocates carton nos. & PI no. to delivery document nos. He creates a packing instruction in SAP.
- SAP packing instruction is handed over to packer for packing.
- After packing a single carton or multiple cartons, the packing instruction sheet with actual packing contents is handed over to SAP user.
- SAP user makes packing modification where required in SAP and prints packing slip.
- Packing slips are inserted in the corresponding cartons and cartons are placed in loading bay.
- After all cartons are placed in loading bay, invoice in created in SAP using VF01 and vendor posting is done using MIRO. All relevant documents are printed and handed over to driver.
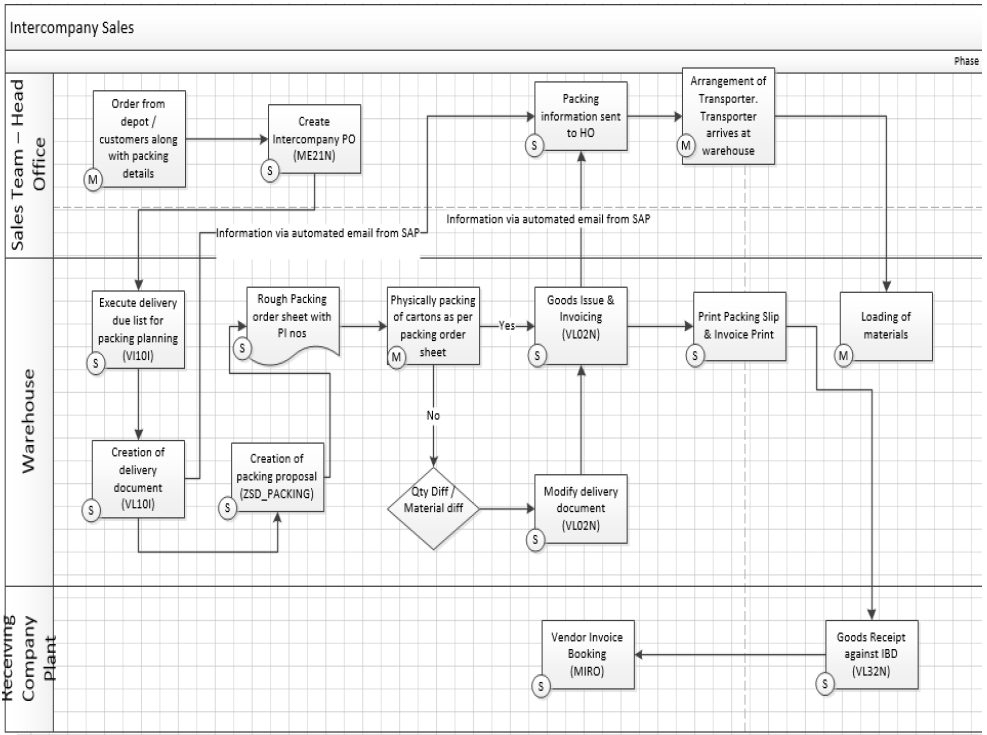